CASE STUDY
Collaborative Insulation Install Makes Difference for Historic Neighborhood Development
Union at the Grove
Choosing the right insulation materials is critical for any construction project no matter the size or scope. When it comes to multifamily apartments, it is especially vital to select the right materials up front – to maximize occupant safety, and for long-lasting performance with minimal maintenance for the many families residing inside.
The Union at the Grove, a set of six sister apartment buildings in St. Louis, was designed to cater to younger families and working professionals alike. The project combines market rate housing with attainable workforce housing. The objective from the start: Select and install the optimal insulation solution to ensure the long-term comfort of tenants for years to come with little to no intervention needed from property management.
Based on the complex’s location, material selection was only one part of the complex matrix for this project.
Since its late 19th-century days of serving nearby working-class residents, The Grove has evolved to become one of the Gateway City’s most eclectic and progressive neighborhoods. With such history comes a neighborhood layout that is less suited for modern-day buildings and the techniques associated with their construction.
When St. Louis-based Green Street Real Estate Ventures was searching for an insulation partner who would not only install a quality product but also remain flexible when it came to the project’s specific development conditions, they turned to Midwest Insulation LLC.
A Challenging Installation
Alongside the typical factors that come with building in an older, historic neighborhood, this project also saw logistical challenges such as narrow streets, tight pathways, and crowded building sites.
The project was in a tight spot, physically,” said Mike Benfatto, commercial manager at Midwest Insulation. Green Street was looking for someone who would also be flexible when it came to worksite logistics. Our crews were happy to oblige, and we worked alongside other contractors to ensure the project remained on schedule. It was challenging, but we found a way and got it done.”
With Midwest being a Goley partner and an Owens Corning® Certified Energy Expert®, Green Street knew they could expect a reputable installation that would deliver optimal thermal performance for tenants and stand the test of time for management.
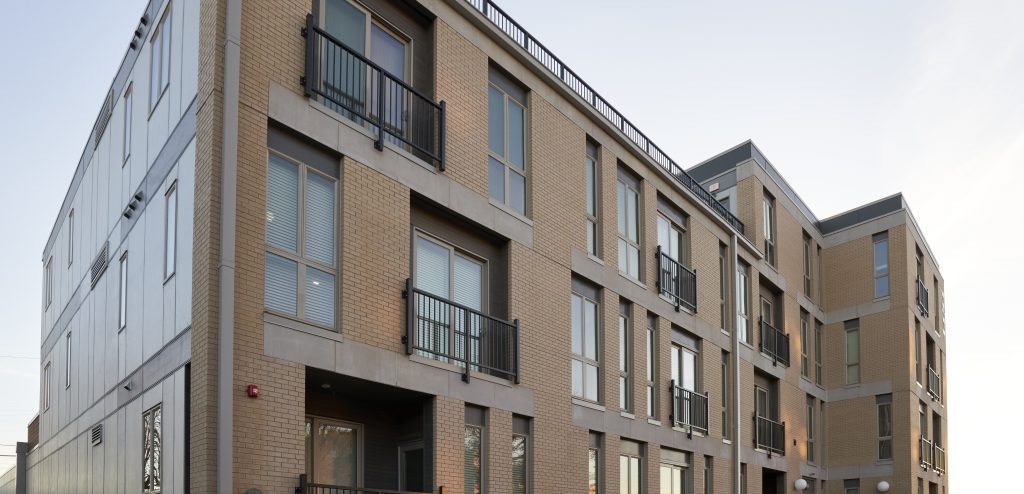
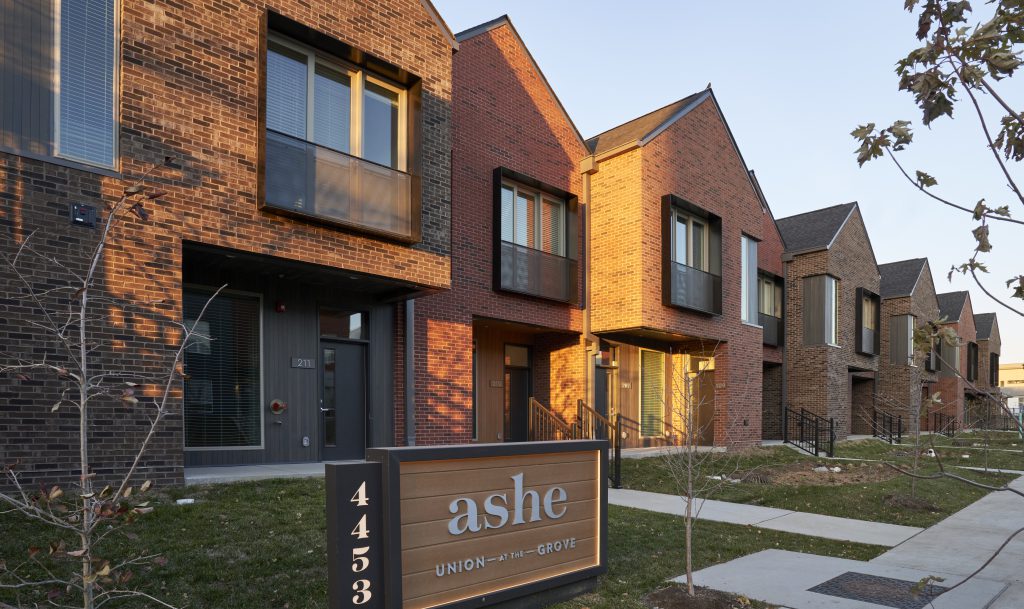
Reducing Fire Risk
Being a multifamily apartment complex, the Union at the Grove needed to be able to withstand the risks associated with potentially hazardous situations. A big consideration for this is ensuring a proper fire barrier is in place.
The fiberglass insulation we used allowed us to limit the number of sprinklers in the building’s internal system,” said Benfatto. “Our full-fill fiberglass installation serves as a fire barrier in such an event. Therefore, the amount of sprinklers needed and where they’re placed throughout the building changes. In sum, it makes the building safer.”
Midwest relied on Owens Corning® SafeStainable PINK Fiberglas™ batt insulation throughout the six buildings. Additional blow-in, loose-fill insulation between floors and truss cavities allowed voids to be completely filled.
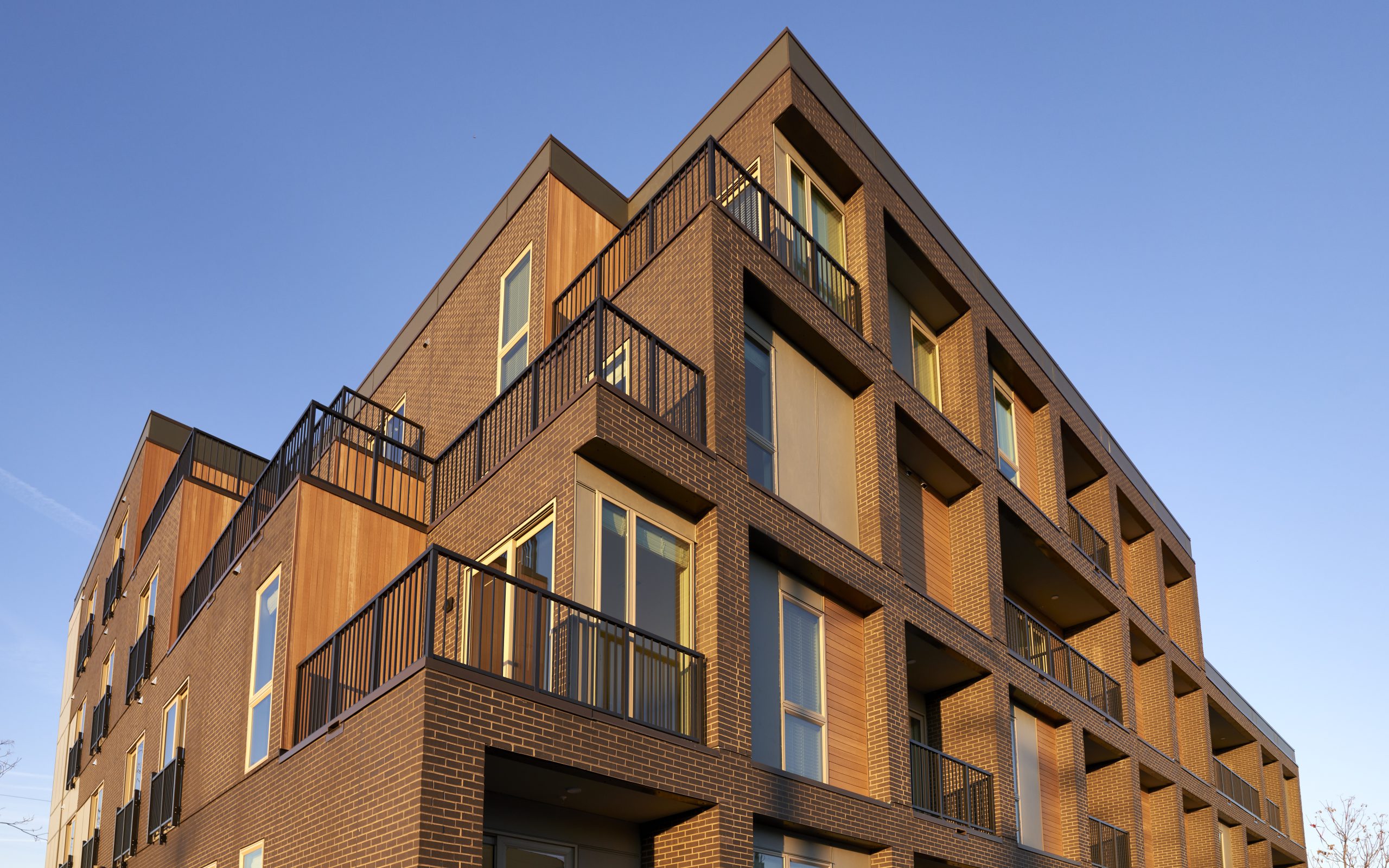
Problem Solving
During the installation, Midwest encountered a challenge with netting for the blown-in insulation. Because of the project’s tight footprint, the Midwest team had to work hand-in-hand with the project’s on-site framing crew so as not to interfere with their respective installations.
Challenges also arose when certain portions of the overall build were not complete when Benfatto and his team arrived on site.
There were occasions when we had to be educators or students with other contractors on the project,” said Benfatto. “Coordinating schedules and installations was a real challenge at times. But in the end, the client’s satisfaction was our priority, and we were able to ensure a quality installation while coordinating with a number of different trades, including plumbing, mechanical, and electrical.”
Midwest needed to adjust to an ever-changing project schedule, and even had to re-net portions of the walls, floors, and other cavities to prep for blow-in insulation. The organization’s expertise and quality of work ultimately overcame specific challenges that arose throughout.
We are no stranger to construction challenges,” added Benfatto. “The most important thing is getting the job done right. In the end, we did that.”
A Polished Result
Thanks to Midwest’s open collaboration with builders and other trades, the Union at the Grove was completed on time and on budget.
A ribbon-cutting ceremony in Nov. 2022 marked the opening of the development. Studio, one-, and two-bedroom units are available alongside two-story row homes. Private entrances, bike storage, barbecue areas, and rooftop terraces are just a few of the many amenities available to tenants.
Project Stats
PRODUCTS
300,000 square feet of Owens Corning® SafeStainable PINK Fiberglas™
150,000 square feet of Blow-In loose-fill insulation
# CREW MEMBERS
8 Midwest crew members
TIMELINE
February 2021 through November